Not all waterjets are created equal. Do your homework before making a purchase.
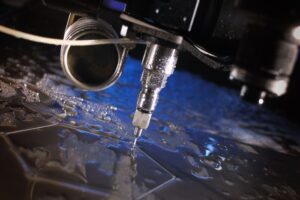
A waterjet cutting machine is a complex piece of machinery with several key components, such as a high-pressure pump, nozzle and control software. But it doesn’t end there! There are many things to consider before purchasing a waterjet, from cutting speeds to service to resale value. Here are ten things to think about before buying your waterjet.
1.Pump Technology: which pump is best?
There’s a longstanding debate about which pump is best, crankshaft direct drive or intensifier. It really depends on your cutting environment and needs.
If you are only cutting with water, then pressure is your best friend. If you are cutting with abrasive garnet, it’s the horsepower getting to the nozzle that counts, not the PSI.
Why use a crankshaft direct drive pump?
Crankshaft direct drive pumps use a crankshaft to move plungers that pressurize the water. In the absence of a hydraulic system, crankshaft pumps offer higher efficiency, increased horsepower and pressure consistency for better part quality.
With a crankshaft direct drive, you run at 95% efficiency, meaning that 95% of your horsepower is getting to the nozzle. You enjoy more cutting power per dollar, lower operating costs and higher overall efficiency.
Why use an intensifier pump?
Intensifier pumps use hydraulics to pressurize the water. They run at 65% efficiency, meaning that only 65% of your horsepower is getting to the nozzle.
An advantage to intensifiers is that you can run multiple machines from a single pump. They can maintain a relatively constant pressure output at one machine while a nozzle on another machine is being turned on or off. In a water cutting environment, you can add more nozzle to get the job done. However, intensifiers tend to run hot, in which case you would need a chiller in a close loop to cool the hydraulics (added cost).

2. Control Software: is it suited to your machine?
You can have the fastest car in the world, but if you don’t have the right driver, you aren’t going to get anywhere. Same goes with waterjet software: if you don’t have the right software for the machine, you won’t get very far. Make sure that the software is waterjet-specific and can handle all the different materials you want to cut.
Likewise, the control software dictates cutting speed, depending on how well it predicts, compensates and optimizes for jet behaviours in various configurations. In other words, skimping on software will cost you in other ways.
Moreover, software upgrades over the life of your machine will improve accuracy, provide faster cutting speeds, enhance system monitoring and provide additional waterjet cutting capabilities, ultimately helping you to remain competitive and control operational costs.
3. Motion System: can it handle your cutting environment?
Choose a machine with a motion system designed to withstand exposure to water and abrasive.
Ball screws and rack and pinion aren’t suited for such a harsh environment and require extra care to properly seal all components.
Instead, opt for a motion system specifically designed for a waterjet environment, such as the Omax Intelli-TRAX AbrasiveJet Linear Drive system. Used worldwide, it offers 1-micron resolution for incredible accuracy, smooth motion, waterjet robustness and low maintenance.
4. Operating Costs: how much will it cost to run per day?
Operating costs can vary greatly between manufacturers. Be sure to check the cost of consumables (water, electricity, sewer, abrasive), spare parts and labour.
Get multiple manufacturers to cut the same sample part and add up their costs. You may notice a variance due to the efficiency of the path planning algorithms, nozzles and pump used, etc.
Talk to others who are using the machine in question to get their feedback. Ask about operating costs, tech support, level of service, access to local parts and so on.
5. Documentation: is it user friendly?
No one ever really thinks about how important a user manual is until something goes wrong! The importance of good documentation cannot be understated, especially when you need to look something up in a hurry or train a new operator.
Some manufacturers try to cut corners when it comes to documentation. That’s why it is important to see if the information is clearly presented and explained before purchase. Are there illustrations? Is it easy to understand? Does it clearly explain how to perform basic maintenance?
6. After Sales Support: is the manufacturer there for you?
Does the manufacturer offer reliable customer service? Where is it coming from? Do they quickly and efficiently resolve issues? Talk to your colleagues about their experiences with the manufacturer.
How about training? Basic training is generally offered upon installation, but what about a month or so down the road, after you’ve been using the machine for a while? Follow-up training is especially beneficial to your bottom line as your employees develop their expertise. If you purchase accessories, be sure to arrange the training required to operate them properly and optimize performance on your investment.
7. Resale Value: how does the brand rate on the used market?
Resale value is a good indication of quality when it comes to waterjet machines. Check out the market to see where different brands rank in terms of price. Those selling for more on the used market generally denote good durability and a strong brand reputation.
8. Sample, Test, Measure, Repeat!
When looking at different machines, it is vital to directly compare machining times, accuracy and finish quality.
First, take your part specifications to different manufacturers and get them to cut samples from the same material. Watch the process from start to finish, from drawing to the finished part, and measure the dimensions accurately (especially the corners).
Look for “witness marks” that could indicate poor feed rate control, sensitivity to vibrations, or other machine problems. They may also be caused by deep scratches in the surface of the material, or the pierce point.
Then, check for repeatability by making several of the same part in different spots of the machine. Compare for accuracy.
9. Cutting Rates: what speed range do you need?
Unless you are only cutting large squares, linear cutting rates won’t be of much help to you. Machining operations require a slower cutting speed for precision and surface finish, especially for corners and radii.
When it comes to cutting, faster isn’t always better. The quality of the part will depend largely on the speed at which it is being cut. Instead of asking, “How fast will it cut?”, you should be asking, “How long will it take to cut this part to X tolerance?”. Again, watch as they cut.
For abrasive jet machining, it is rarely necessary to go over 100 inches per minute (25 m/min). This is because your main limiting factor will be the cutting speed of the abrasive jet cutting process. You may want the machine to go a little faster than this during traversing, but the traverse speed will play a very minor role compared with the cutting speed.
For pure waterjet cutting (water only), you will want go faster. If you do primarily water-only work, you may want a machine as fast as 300 inches per minute (76 m/min) or faster. If you only do a little water-only cutting, do not worry about maximum speed.
10. Deals: where to look?
There are legitimate deals to be had on waterjet machines – you just need to sniff them out.
Consider buying demo units or prototypes. Pick up a demo from a trade show (you might need to reserve ahead of time!). With what the manufacturer will save on shipping the unit back to the warehouse, you could very well get a great deal. Of course, refurbished machines are always a viable option.
When to buy
It’s generally a good time to buy during a slow economy. Manufacturers might have an inventory surplus that they would gladly get rid of.
How to save
Check with your advisor to see if there are tax advantages for purchasing equipment or training grants available. Every little bit helps!
For More information visit : www.spark-co.com