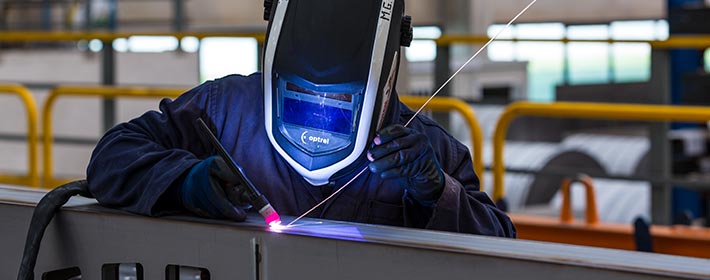
Understanding Welding Methods: Laser Welding vs MIG and TIG Welding
Welding is a crucial process in the manufacturing and fabrication of various products, especially in the metalworking industry. However, there are several types of welding methods, each with its advantages and disadvantages. In this article, we’ll focus on three popular welding methods, i.e., laser welding, MIG welding, and TIG welding, to understand their differences and when to use them.
Different Welding Methods
Welding is a process of joining two or more materials, typically metal parts, to form a permanent bond. There are several welding methods, including:
MIG Welding
MIG welding, or Gas Metal Arc Welding (GMAW), is a welding process that uses a continuously fed wire electrode and a shielding gas to create an arc between the wire and the material being welded. As the wire melts, it forms a pool of molten metal that fuses with the base material, creating a strong and durable bond.
This traditional welding method is a popular welding process in the manufacturing industry, especially for the production of automobiles, bikes, and other machinery. This is because MIG welding is a fast and efficient method of welding, capable of producing high-quality welds in a relatively short period of time. Additionally, MIG welding is relatively easy to learn compared to other welding methods.
In MIG welding, the wire electrode is continuously fed from a spool through a gun, while a shielding gas is continuously pumped through the gun to protect the weld from oxidation and contamination. The shielding gas also acts as a coolant to prevent the weld from overheating.
One of the advantages of MIG welding is that it can be used to weld a variety of materials, including aluminum, steel, stainless steel, and other alloys. Additionally, MIG welding is a relatively efficient process, which means that it can be used for high-volume production runs.
However, MIG welding does have some disadvantages as well. For instance, it is not suitable for thin materials or materials with high heat distortion. Additionally, MIG welding can be challenging to use outdoors or in windy conditions, as the shielding gas can be easily blown away.
Overall, MIG welding is an excellent welding method for manufacturers who need to produce a high volume of products with consistent quality. While there are some disadvantages associated with MIG welding, these can be mitigated with proper training, equipment, and operating procedures.
TIG Welding
TIG welding, or Gas Tungsten Arc Welding (GTAW), is a precise and complex welding process that uses a non-consumable tungsten electrode to create an arc between the material and the welding machine. This process also requires shielding gas to protect the weld zone from contamination and oxidation.
TIG welding can produce incredibly precise and intricate welds, making it ideal for applications in aerospace and medical industries where high-quality welds are essential. Additionally, TIG welding can be used on any type of metal, including steel, aluminum, copper alloys, magnesium alloys, and more.
One of the main advantages of TIG welding is its precision. The tungsten electrode creates a very fine electrical arc that enables welders to recreate intricate shapes with great accuracy. Furthermore, TIG welding produces strong and durable welds that are resistant to corrosion and have good fatigue properties.
However, TIG welding does have some drawbacks as well. For instance, it has relatively low productivity compared to other methods such as MIG welding. Additionally, it requires complex equipment which makes it difficult to use in remote locations or outdoors. Moreover, TIG welding is often considered difficult for beginners or inexperienced welders due to its complexity.
In conclusion, TIG welding is an excellent choice for manufacturers who require precise and intricate welds on various materials such as steel, aluminum alloys, copper alloys etc., especially when working in aerospace or medical industries. While there are some drawbacks associated with this method of welding, proper training and operation procedures can help mitigate these shortcomings while still producing high-quality results.
Laser Welding
Are you in search of a high-tech welding process that guarantees precision and aesthetic appeal? Fiber Laser welder is the solution you need! Laser welder involves the use of a focused laser beam that melts and fuses the materials together, resulting in a perfect and seamless finish.
Laser welder is used in various industries, including the jewelry and microelectronics industries, thanks to its precision and ability to produce aesthetically pleasing welds. Compared to traditional welding methods, which are slower and less precise, laser welder is up to 4to 10 times faster and can weld a wide range of materials up to ¼” thick. This high productivity rate reduces production time and ultimately saves cost.
Furthermore, fiber laser welders are ideal for dissimilar metal welding, joining pieces of metals or thermoplastics through the use of a laser welder, making it a non-contact welding process that requires access to the weld zone from only one side of the parts being welded. This unique feature allows for various joint geometries, and it is not limited to just steel; it can weld aluminum and copper materials.
Whether you’re in the fabrication industry, jewelry business, or microelectronics field, fiber laser welding is a high-tech process that offers precise welds, aesthetic appeal, faster production rate, and reduced production cost. Choose laser welder today and watch your production process transform for the better!
Learn more about handheld laser welders and cleaning systems here, the benefits of laser welding here, and how laser welding works here.
Comparing Welding Methods
To help you understand when to use each welding method let’s compare them on various parameters
Advantages and Disadvantages of Each Welding Method
MIG Welding
Has the following advantages :
- High welding speed
- Easy to learn
- Can be used on different thicknesses and materials épaisseurs et matériaux
- Has the following disadvantages :
- Not suitable for thin metal sheets
- Poor penetration
- Not highly precise
TIG Welding
Has the following advantages:
- High precision and quality
- Can be used on various materials
- Good for thin metal sheets
- Has the following disadvantages:
- Slower welding speed
- Not suitable for thick materials
- Difficult to learn
Laser Welding
Laser welder has many advantages over traditional welding processes. It is faster, up to four to ten times faster than those traditional methods, and produces a much more precise weld that requires less cleanup or grinding afterwards. Additionally, fiber laser welder requires access to the weld zone from just one side of the materials making it ideal for joining pieces of metals, dissimilar metals welding, thermoplastics and for creating unique joint geometries.
Compared to traditional welding methods, fiber laser welder involves no contact between the material being welded. This allows laser welder to be used in tight spaces and on thin materials that are not suitable for other types of welding. Also, because the intense heat is focused on a small area, there is less risk of distortion in the material surrounding the weld zone and can weld dissimilar metals.
Another benefit of fiber laser welder is that it can weld a wide range of materials including steel, aluminum and copper alloys up to ¼” thick. Additionally, due to its high precision, it can be used for intricate projects such as jewelry making or microelectronics where aesthetics are important.
Finally, due to its increased speed and precision, laser welder often results in reduced production time and costs compared with traditional welding techniques. All these benefits make fiber laser welding an attractive option for businesses across various industries such as fabrication, jewelry design and microelectronics.
What gas do we use with laser welding?
Laser welder typically uses an inert gas such as Argon, Helium or Nitrogen in order to protect the weld zone from any unwanted contaminants. In some cases, a combination of these gases may be used depending on the material that is being welded and its desired properties. The inert gas also helps to create a more consistent weld line when welding metals and can reduce spatter which makes cleanup considerably easier. Having the right gas blend for laser welding is essential for achieving an optimal weld so it is important to ensure that only high quality gas mixtures are used whenever possible.
Nitrogen :
Nitrogen is one of the most commonly used gases for laser welder as it can provide a number of benefits for welded components. It can be used in both argon and helium mixtures, depending on the desired result. Nitrogen helps to protect the weld zone from unwanted contamination, reduce spatter and improve the quality of the resulting weld. It is also often used when welding large surfaces or creating thicker joints as the nitrogen can help to create a more consistent heat distribution, resulting in a stronger bond between two metal surfaces.
Argon :
Argon is typically used when welding aluminium or smaller components or when precision is critical. It acts as an inert gas, shielding the weld zone from corrosion and preventing oxidation during the welding process. Additionally, it helps to protect the metal from impurities, providing a cleaner finish with reduced spattering. The use of argon can also result in a more precise weld since it provides greater control over heat distribution and stability within the weld area. Moreover, it is often used for fine detail work such as jewelry making or microelectronic assembly.
Helium :
Helium is an inert gas that is often used for welding of lightweight materials such as aluminum and magnesium. The main benefit of using helium is that it provides a much hotter flame, allowing the user to weld more quickly and easily. Additionally, it helps to reduce heat loss, which can result in a stronger bond between two metal surfaces and less distortion in the weld area. For this reason, it is often used in applications where speed and precision are important such as pipe fitting or automotive repair work.
Laser welder has the following advantages:
- High precision and quality welds
- Ideal for fine welds on small parts
- Short welding time
- Less distortion
- However, laser welding has the following disadvantages:
- Bigger initial investement.
- Not suitable for thick materials
- Difficult to repair the weld once done.
Choosing the Right Welding Method
Choosing the right welding method depends on various factors such as the industry, material thickness, budget, and quality. For example, MIG welding is suitable for the automotive and construction industries, whereas TIG welding is ideal for aerospace and medical industries. Laser welding, on the other hand, is perfect for microelectronics and jewelry industries.
Before choosing the welding method, consider the material thickness, joint type, and production volume. If the material is thin and high precision is required, then TIG or laser welding is preferred. For thick materials, on the other hand, MIG or laser welding is a better option.
Conclusion
Welding is a complex process that requires knowledge of various welding methods and their application areas. MIG, TIG, and laser welding are popular and effective methods with unique advantages and disadvantages. Choosing the right welding method depends on several factors such as the industry, material, precision required, and budget. Understanding the differences between welding methods can help manufacturers make informed decisions and choose the best method for their specific use case.
Source:
https://www.sme.org/technologies/articles/2019/october/traditional-versus-laser-welding/
https://lasersystems.ipgphotonics.com/Applications/Laser-Welding